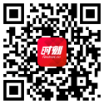
“抓住”跑掉的能源
看华菱湘钢如何将余气、余热、余压“吃干榨尽”
制图\李妍
湖南日报记者 黄利飞
焦炉炼焦、高炉炼铁、转炉炼钢、轧钢成材……钢铁炼成需经上百个工序,全程会消耗大量能源资源,同时也会产生大量的余气、余热和余压。
以前,余气、余热和余压都被当作生产的废弃物白白浪费掉了。华菱湘钢能源环保部首席工程师吴畏告诉记者,上个世纪80年代,湘钢有一盏“天灯”十分引人注目——厂区内1座50米高的煤气放散塔顶端,因煤气燃烧“蹿”出3米高的蓝色火焰,像悬挂在空中的大灯,日夜不熄。
“那时候煤气燃烧放散,在钢铁厂是再正常不过的事,大家只觉得‘天灯’景象壮观,没有人意识到这是一种能源浪费。”吴畏说。
11月6日,记者来到湘钢厂区,煤气放散塔静静矗立,顶端没有了烟雾,更没有火苗。
吴畏介绍,上世纪90年代初期,湘钢在轧钢过程中,将钢坯加热炉燃料“以气代油”,即用煤气代替重油来烧坯,公司煤气放散量逐渐减少。
“天灯”彻底“消灭”在2015年1月。标志性的事件是湘钢第二台135兆瓦高温超高压发电机组投产运行。
135兆瓦发电机组主要是利用余气发电。高炉炼铁产生的煤气,一部分供炼铁自用,多余部分被“赶”进管道;煤气经管道进入锅炉燃烧,加热水使水变成过热蒸汽;过热蒸汽推动汽轮机旋转,带动发电机发电。
湘钢超高压余能发电车间副主任陈仕介绍,135兆瓦发电机组操作系统很复杂,2013年第一台机组刚装上时,会控制系统的人屈指可数,熟练的人更是少之又少!
原来,湘钢上135兆瓦发电机组时,国内只有1家钢厂有1台相同功率的发电机组运行。“当时,那台机组运行得还不太稳定,对湘钢来说,没有师傅带,也无经验可寻。”
陈仕介绍,为了让技术人员尽快熟悉操作系统,湘钢特意搭建起135兆瓦发电机组仿真培训中心;最初两年,每名操作人员每天要在仿真室模拟操作系统上“工作”1个小时。
置身湘钢超高压余能发电车间,机器轰鸣作响,银白色管道纵横交错。
车间分上下两层,第一层多台蓝色水泵并排而立,第二层主要是汽轮机、发电机和实时监控室。
在实时监控室,记者看到,一台135兆瓦发电机组共有45套系统,每一套系统下面又包含若干个子系统,“一般要学习1至2年,才能掌握整套系统的操作。”陈仕说。
超高压余能发电车间外,连接着变压器、升压站、输电线路,俨然一座小型发电站。
目前,余气发电量占到湘钢自发电总量的85%,是绝对“主力军”;余热发电量和余压发电量,分别占比14%和1%。
余热发电,主要是利用冶炼烧结矿石时产生的热量来发电。湘钢配置的是1台4.5兆瓦和1台20兆瓦的发电机组。
余压发电,主要利用煤气从高炉炉顶(煤气压力约为220千帕)到管网(煤气压力约为15千帕)这个过程中产生的压差发电。湘钢4座高炉配置了4台发电机组,功率在15兆瓦到20兆瓦不等。
余气、余热、余压的综合利用,使湘钢自发电量逐年提升并屡创新高。
2011年,湘钢自发电量13.6亿千瓦时,占企业总用电量的35%,处于行业较低水平。
往后逐年提升:2014年23.5亿千瓦时,2015年29亿千瓦时。
2016年跃升至31亿千瓦时,自发电量在企业总用电量中所占比例增加到85%以上,跻身行业先进水平。生产不饱满时,自发电消耗不完,还向湘潭电网返送电能。
2017年,湘钢自发电量达31.1亿千瓦时。也正是这一年,湘钢能源精细化管理模式获得了全国优秀能源管理案例奖,成为全国钢铁企业中唯一获奖的单位。
今年,湘钢日均自发电量达904万千瓦时,年自发电量预计可达33亿千瓦时。“外购电成本约0.6元/千瓦时,以此计算,湘钢自发电今年可创效益近20亿元。”
吴畏介绍,湘钢能源环保部已经对整个厂区的高品质余热做了全方位“扫荡”,发现目前只有焦炉烟气上升管的余热、3个轧钢加热炉产生的余热,还没有回收利用。
针对此,湘钢能源环保部已经制订了相关计划,准备上第三套高效发电机组,可研性报告已递交华菱总部,获批后即实施。